Reduced Cost per Mailed Document
From Scott Gerschwer, Ph.D., Compart NA Marketing
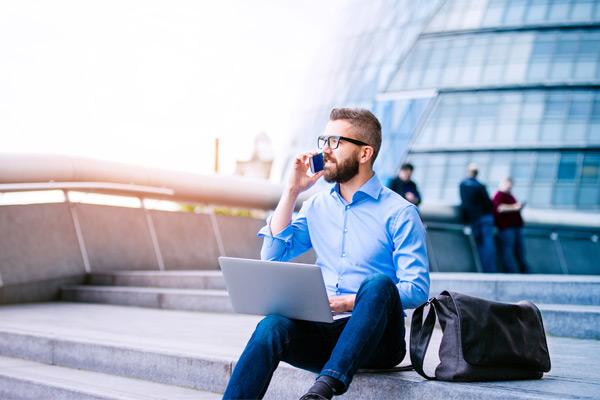
Centralization of Individual Correspondence: A Case Study
Your business, your rules. Your business rules.
With a diversity of insurance products and a mission to offer customers the best quality individual service, Insurance Company I* had a strong need for individualized correspondence.
Let's face it, not all business transactions can be finalized using standard documents and forms. Examples include contract change inquiries, confirmation of benefits and premium adjustments. In each case, the responsible correspondent selects the appropriate procedure, crafts the message and sends the message. Very often this happens by mail. But one thing is consistent and clear: based on individual customer concerns, the message is as specific and wide-ranging as can be imagined. It can also be pretty tedious stuff.
In the past, this level of individualization meant that an administrator had to handle the tasks of printing, adding inserts, enveloping, addressing and franking. These administrators cried out for relief, process improvement, and automation of the workflow. And in the end, it was these administrators who initiated the project. They wanted to work more efficiently, freed once and for all from the "burden of extraneous tasks" so they could handle high value stuff and leave the crap work behind.
So the company set up a document processing workflow to link individual correspondence with the production print/mail operation it already managed. As one of the larger document producers in the world, the logical next step was to embed individual correspondence into their central, automated document production.
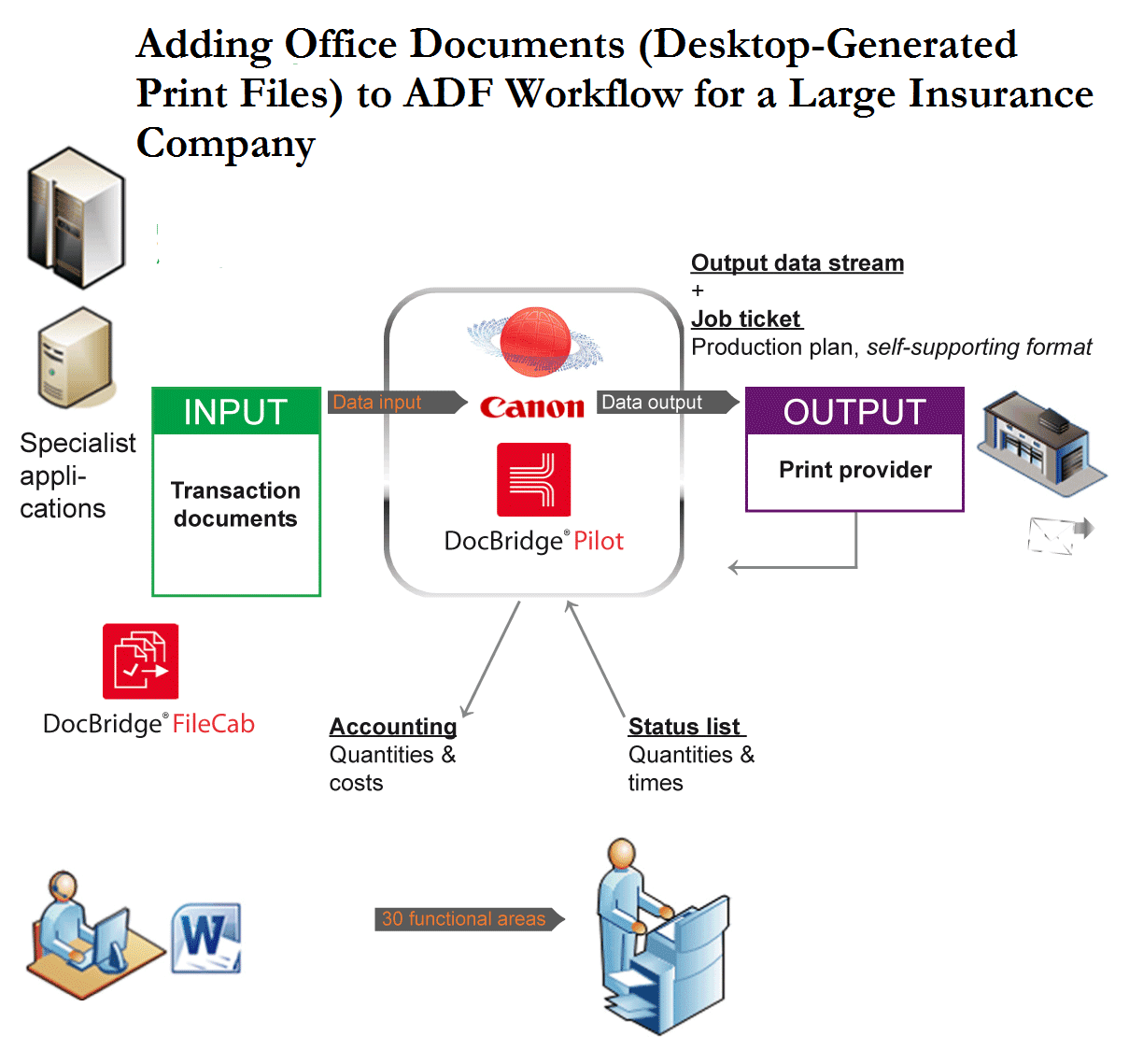
First, a look at the workflow process and structure: two highly specialized applications – comparable to an Enterprise Resource Planning (ERP) system – are used to run their core business processes. These are linked to a central system for document creation, which generates millions of documents; contracts, policies, allowance applications, bonus and value notifications, etc.
At the nexus of these applications and their main print provider (the company has outsourced document production for a decade) is an output management system (OMS) designed by Canon that receives, identifies, and classifies all generated documents and adds additional information as needed, such as control codes for inserts, enveloping, franking, etc. Within this output management system is the COSMOS solution, a comprehensive workflow management system, also developed by Canon. A third-party solution supplies the OM technology to prepare the documents for production and mailing.
The OMS generates standardized metadata that provide the print service provider all the information needed for automated production (printing, bundling/sorting, adding inserts, enveloping, franking, handover to postal provider). The company and the print provider agree on clearly defined handling rules (e.g., same-day document printing and mailing) and status lists are automatically generated for mutually monitoring their service level agreement (SLA).
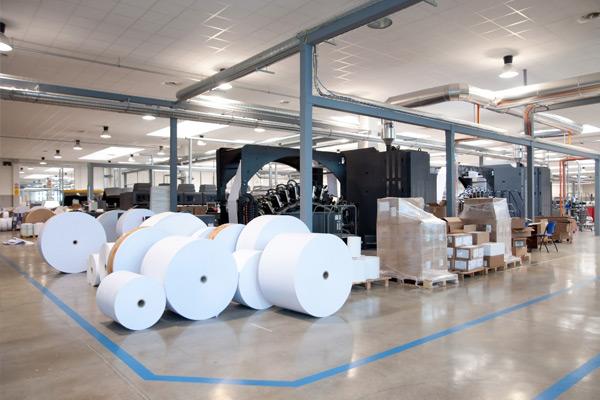
This was all set up for batch processing. But what about the individual correspondence?
In principle, the workflow is the same with one exception: the documents originate in a Microsoft Office program and not a special application. Using MS Office, admins select the document template appropriate for the business transaction from a "digital template cabinet" stored in the system and fill in the recipient address and other process-specific fields.
But then, when they go to print the document, they now select DocBridge® FileCab from the list of available printers. Filecab acts like a print driver: a dialogue box opens with the user-specific functions and features needed for automatic processing. The admins can check the document against various functional and technical criteria (correct spelling and position of the address, accurate reference line, compliance with corporate brand identity elements, fonts, graphics and logos, etc.), include case-related comments, and add static inserts (PDF files) that are have been validated company wide.
If everything is correct and complete, the individual letter is sent to the archive and the central OMS. From there, the workflow is the same as for bulk processing (transaction documents). The workflow is set up so that DocBridge® FileCab collects the documents created on approximately 600 PC workstations -- inside and outside -- and transmits them to the output management system, which is a combination of DocBridge® Pilot and COSMOS. From there, they are centrally processed.
Process reliability, first and foremost
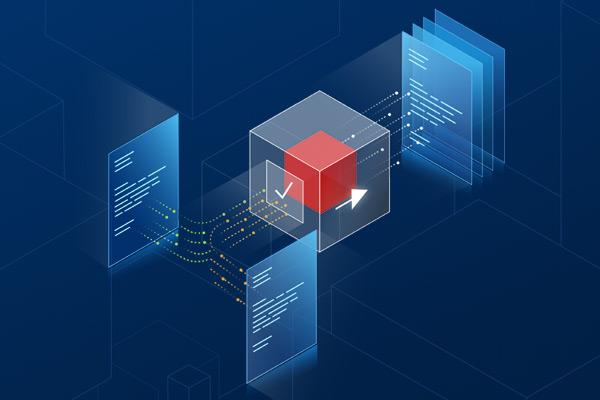
Since this workflow was established, processing times in the individual departments have dropped dramatically. Gone are the days of employees running back and forth to the department printer. Only in rare cases (e.g., for registered mail) are documents still produced locally. Otherwise, everything is automated.
And greater productivity is just one benefit. The major advantage of modernization is process reliability. "Keep the fingers off the process" is how one manager described it. Now even individual correspondence is subject to quality checks during the document creation process, which takes the pressure off the admins. Embedding local correspondence into automated standard processing has significantly reduced the risk of selecting the wrong template, adding an out-of-date insert, or using an invalid address.
ROI has actually been achieved with only the initial group of admins participating. The company continues to roll out DocBridge® FileCab to employees at the home office and out in the field to add to their list of available printers on their PCs so that as many documents as possible that are designed to be printed, mailed or archived for online viewing are placed into the document output management system.
About Compart:
The company, headquartered in Germany, has been a market presence for over twenty-five years and has subsidiaries in Europe and North America as well as a network of partners in Latin America, Africa and Asia.
Compart helps companies boost the efficiency of their operations with solutions for quick and flexible processing of high-volume data streams and document quantities. The scalable and platform-independent DocBridge® family of products, designed, developed and supported by Compart, allows documents to be output anytime, anywhere, digitally or on paper.
The company enjoys a worldwide reputation as an innovative market leader as well as a developer of professional and leading-edge solutions in the field of content and document technology. More than 1,200 customers in 42 countries rely on Compart solutions, in industries that range from finance, insurance, and retail to printers, telecommunications, utilities and healthcare.
Furthermore, Compart is a technology partner for some of the leading manufacturers in the industry. Our software is embedded within some of the most often used Multi-Function Devices, printers and copiers in the world and is considered reliable and relatively maintenance-free. If we can do it for those amazingly high volumes we can do it for you.
*This is a masked case study because the insurer in question views the capability described as a strategic asset and does not want to alert competitors. We at Compart respect the need for privacy of our customers and will not reveal our sources. If you would like to know more about the solution described (but not the company involved) please contact us at info@compart.com or click here for a FREE white paper download.